Hey there, my friend! Let’s dive into the fascinating world of terminals and wire harnesses in vehicles. Did you know that terminals are like the superheroes of electrical connections? They ensure our cars stay safe and reliable, and that’s no small feat!
Contents
- 1 I. Understanding Terminals in Automotive Wiring Harnesses
- 2 II. Terminal Selection and Application
- 3 III. Terminal Installation in Automotive Wiring Harnesses
- 4 IV. Terminal Maintenance and Repair
- 5 V. Advancements and Innovations in Automotive Wiring Harness Terminals
- 6 VI. Future Trends and Challenges in Terminal Applications
I. Understanding Terminals in Automotive Wiring Harnesses
A. Definition and Role of Terminals
So, what exactly are terminals? Well, they’re these nifty little connectors that link electrical wires to all the electrical gizmos in our beloved vehicles. They play a crucial role in establishing solid connections, making sure those electrical signals and power flow smoothly throughout the car’s system. Think of them as the bridge that brings everything together.
B. Different Types of Terminals Used in Automotive Harnesses
Now, terminals come in different shapes and sizes, each with its own special powers. Let me introduce you to a few of these mighty connectors:
1. Blade Terminals
These bad boys, also known as spade terminals, have a flattened metal blade that fits snugly into a female connector. You’ll often find them chilling in fuse or relay boxes, providing fast and reliable connections that are vital in those situations.

2. Ring Terminals
Picture this: circular connectors that attach themselves to bolts or studs, creating a strong and durable bond. These ring terminals are the go-to when it comes to grounding wires and other scenarios where a robust connection is a must. They’re like the bodyguards of the electrical world!

3. Spade Terminals
These terminals have flat metal blades with prongs that resemble forks. They’re all about quick and secure connections. Perfect for speaker hookups and sensor wiring, they get the job done in no time.

4. Butt Connectors
No, it’s not a connector for your backside! Butt connectors are tubular terminals that ensure secure wire splicing, all while shielding against environmental hazards. They’re like the protective armor of the electrical world, guarding against any potential threats.
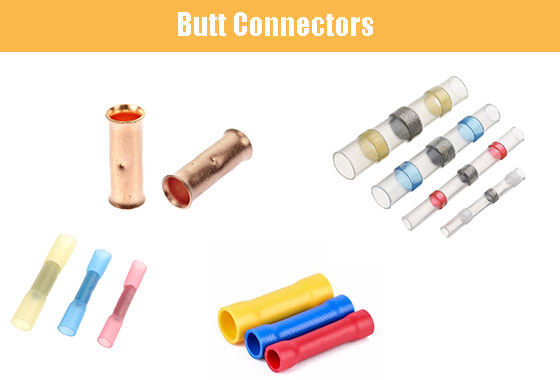
5. Bullet Connectors
Sounds dangerous, right? Well, these cylindrical connectors are actually quite helpful. They consist of male and female components that fit together like a puzzle, creating connections for lighting systems and sensors. They’re the bulletproof vests of the electrical world, keeping everything in line.
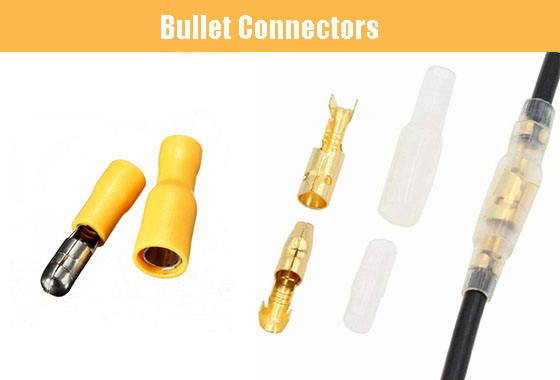
6. Pin Terminals (male terminals)
Time to meet the pin terminals! These pin-like structures are masters at connecting electronic control units (ECUs), sensors, and other electrical components in wiring harnesses. They establish a reliable signal and power transmission interface, fitting snugly into female sockets and ensuring a rock-solid connection.
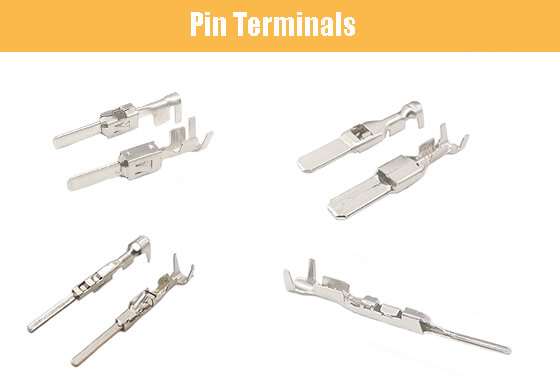
7. Socket Terminals (female terminals)
Last but not least, let’s not forget about the lovely socket terminals, also known as female connectors. They play a crucial role in establishing accurate and secure connections with pin terminals. You can think of them as the welcoming hostesses, providing the perfect meeting point for pin connectors.

C. Construction Materials for Terminals
Depending on their needs and use, terminals are often built from various materials. The following materials are frequently utilized in terminal construction:
1. Copper Terminals
Due to its outstanding electrical conductivity, copper terminals are frequently used in vehicle wiring harnesses. Low electrical resistance provided by copper ensures effective power transfer while lowering the chance of voltage loss.
2. Aluminum Terminals
In some instances where weight reduction is a priority, aluminum terminals are utilized as an alternative to copper terminals. Their lightweight nature and good electrical conductivity make them suitable for specific applications within automotive wiring harnesses.
3. Tin-Plated Terminals:
Terminals featuring a tin-plated coating exhibit enhanced resistance against corrosion, safeguarding them from oxidation and ensuring their longevity. The tin plating is a protective layer, shielding the terminals from external factors like moisture, chemicals, temperature, etc.
II. Terminal Selection and Application
A. Factors to Consider in Selecting Terminals for Automotive Wiring Harnesses
Choosing the right terminals for automotive wiring harnesses demands a thoughtful evaluation of various factors, guaranteeing peak performance and unwavering reliability. Delve into the following key considerations:
1. Current Carrying Capacity
Terminals are no strangers to handling the heat. They must bear the burden of electrical currents without breaking a sweat. Just like a marathon runner pacing themselves, terminals need to be carefully selected to match the current carrying capacity required by the application. Choosing the right terminals ensures they can handle the load without overheating, avoiding performance issues and potential electrical failures.
2. Wire Gauge Compatibility
In the world of terminals, size matters. Wire gauge compatibility is key to establishing a solid connection. Think of it as finding the right shoe size – too tight, and it’s uncomfortable, too loose, and you’ll be tripping over your own feet. Similarly, using terminals that are too large or too small for the wire gauge can lead to poor connections, increased resistance, and safety hazards. Matching the terminal size to the wire gauge ensures a snug fit, securing reliable electrical flow.
3. Environmental Conditions
Terminals face the elements head-on, battling against environmental conditions to maintain a steady connection. Rain, snow, heat, or cold – they endure it all. That’s why terminals often come equipped with protective coatings, shielding them from moisture, chemicals, and temperature variations. By weathering the storm, terminals ensure electrical continuity, even in the harshest of conditions.
4. Vibration Resistance
Imagine hitting a pothole or cruising on a bumpy road. Your vehicle jolts and shakes, but your terminals stay steady. Vibration resistance is a crucial quality of terminals, especially in automotive applications. They need to withstand the constant movement and vibrations that come with driving. By staying firmly connected, terminals ensure uninterrupted power flow, keeping your vehicle running smoothly.
B. Common Mistakes to Avoid when Selecting Terminals
When choosing terminals for automotive wiring harnesses, it is crucial to make informed decisions that optimize performance and reliability. Avoid common pitfalls by considering the following:
– Balancing cost and quality: While cost is a factor, don’t compromise on quality. Base your selection on both affordability and suitability to avoid subpar connections and potential failures.
– Addressing environmental challenges: Account for the automotive environment. Neglecting environmental factors can lead to corrosion, insulation degradation, and electrical issues. Prioritize terminals built to withstand specific challenges.
– Emphasizing wire preparation: Proper wire stripping, cleaning, and preparation are vital for strong connections. Neglecting these steps can undermine the quality of terminations. Follow recommended procedures for reliable and secure connections.
If you want to know more about terminals, you can read the following two articles:
Unlocking the Secrets: Factors Impacting Connector Terminals in Automobiles
C. Tools and Techniques for Terminal Crimping
Accomplishing dependable electrical connections in automotive wiring harnesses relies on precise terminal crimping. Explore the following tools and techniques commonly utilized for this purpose:
1. Crimping Tools
Specially designed crimping tools crimp terminals onto wires, establishing secure connections. Manual, ratchet, and hydraulic options are available. Choose the appropriate tool based on terminal size and application requirements, ensuring consistent and reliable crimps.
2. Effective Crimping Techniques
Employing proper crimping techniques guarantees high-quality results. This involves selecting the correct terminal size, positioning the wire correctly within the terminal, and applying the ideal amount of crimping force. Refer to manufacturer guidelines and specifications for the terminals used, adhering to recommended crimping techniques.
Click The Criteria for Judging The Quality of Terminal Crimping to learn more.
D. Insulation and Sealing Methods for Terminals
To ensure the longevity and reliability of terminal connections in automotive wiring harnesses, appropriate insulation and sealing methods are employed. These methods help protect terminals from moisture, contaminants, and other environmental factors that could compromise the electrical connections. Some commonly used insulation and sealing methods include:
1. Heat Shrink Tubing
Heat shrink tubing, a formidable ally of terminals, adds an extra layer of protection. As heat is applied, this flexible tubing wraps snugly around the terminal, creating an insulating barrier that shields against moisture, contaminants, and physical damage. It not only fortifies the connection but also extends the lifespan of terminals, enhancing reliability in challenging environments.
2. Adhesive-Lined Heat Shrink Tubing
Taking the protective properties of heat shrink tubing a step further, adhesive-lined heat shrink tubing provides a powerful adhesive lining inside the tubing. Once heated, the adhesive melts and bonds tightly, creating a durable seal around the terminal. This ensures not only excellent insulation but also added resistance against vibration and strain, fortifying connections for long-lasting performance.
3. Sealed Connectors
When it comes to durability and reliability, sealed connectors emerge as an unparalleled solution. These specialized connectors, engineered with precision, combine the functionality of terminals with superior sealing capabilities. By creating a secure and impenetrable barrier against moisture, dust, and contaminants, sealed connectors provide a steadfast connection that withstands even the harshest conditions, such as in the engine compartment or exterior lighting systems.
III. Terminal Installation in Automotive Wiring Harnesses
A. Preparing Wires for Terminal Installation
Proper wire preparation is paramount to achieving secure and reliable connections when installing terminals in automotive wiring harnesses. Follow these steps for effective wire preparation:
1. Insulation Stripping
The first step is using wire strippers or a knife to strip the outer insulation without damaging the wire strands. The stripped length should be suitable for the terminal size and crimping requirements.
2. Wire Twisting
In certain instances, wire twisting is employed to enhance wire strength and integrity before terminal installation. Use pliers or wire-twisting tools to twist the exposed wire strands together. This process improves connection stability, mitigates fraying or breakage risks, and ensures optimal performance.
B. Step-by-Step Guide to Terminal Installation
Once the wires are properly prepared, the terminals can be installed following these general steps:
1. Crimping Terminals onto Wires
Begin by positioning the terminal over the stripped wire end, ensuring the wire strands are fully inserted into the terminal barrel. Employ an appropriate crimping tool, matched to the terminal size and type, to apply precise pressure. This deformation securely envelops the wire strands, establishing a robust mechanical and electrical connection. Follow the crimping tool manufacturer’s instructions diligently to achieve a secure crimp without compromising the wire or terminal.
2. Securing Terminals within the Harness
After crimping the terminals onto the wires, they are positioned and secured within the automotive wiring harness. Insert terminals into designated connector housings, route them through assigned channels, or fasten them with cable ties or clamps. Correct positioning and secure attachment prevent strain on the connections, minimize wear due to vibrations, and uphold the overall integrity of the wiring system.
IV. Terminal Maintenance and Repair
A. Common Terminal-Related Issues in Automotive Wiring Harnesses
Automotive wiring harnesses may encounter a range of terminal-related challenges over time. Here are some prevalent issues:
1. Corrosion: Terminals are susceptible to corrosion caused by factors like moisture, road salt, and environmental elements. Corrosion hampers conductivity increases resistance, and potential electrical failures.
2. Loose Connections: Vibrations, temperature changes, or incorrect installation can loosen terminals. Loose connections give rise to intermittent electrical problems, impacting the performance of connected components.
3. Wire Fraying or Damage: With time, wires in the harness can suffer from wear, fraying, or damage. This jeopardizes terminal integrity, leading to poor connections or electrical shorts.
B. Troubleshooting Techniques for Terminal Problems
When encountering terminal-related issues in automotive wiring harnesses, the following troubleshooting techniques can be employed:
1. Visual Examination: Conduct a thorough visual inspection of the terminals and wiring harness, seeking signs of corrosion, loose connections, or wire damage. Look for discoloration, moisture accumulation, or any visible indications of wear and tear.
2. Cleaning Procedure: If corrosion is detected, clean the terminals using an appropriate electrical contact cleaner or a mixture of water and baking soda. Employ a wire brush or a specialized terminal cleaning tool to scrub the terminals gently. Ensure complete drying before re-establishing connections.
3. Secure Fastening: Check for loose terminals and use suitable tools, such as pliers or a screwdriver, to tighten them firmly. Ensuring secure fastening prevents potential future issues.
4. Wire Restoration: For frayed or damaged wires, perform necessary repairs or replacements. Cut out the damaged wire section and employ crimp connectors or soldering techniques to splice in a new section. Apply insulation, such as heat shrink tubing or electrical tape, to protect the repaired area.
C. Repairing and Replacing Terminals in a Wiring Harness
In some cases, repairing or replacing terminals within a wiring harness may be necessary. Here are the general steps involved:
1. Terminal Removal: Use a suitable tool, such as a terminal removal tool or a small flathead screwdriver, to carefully remove the terminal from its connector housing. Take note of the terminal’s orientation and position within the harness.
2. Terminal Repair: If the terminal is salvageable, clean it thoroughly and inspect for any damage or corrosion. Repair or replace any damaged components, such as crimp sleeves or insulation, before reinstalling the terminal.
3. Terminal Replacement: If the terminal is irreparably damaged or corroded, replace it with a new one of the same type and specifications. Ensure proper orientation and alignment when inserting the new terminal into the connector housing.
4. Connection Integrity Check: After repairing or replacing the terminal, perform continuity tests or other appropriate tests to ensure the integrity and functionality of the repaired connection. Verify that the terminal is securely fastened within the connector housing.
V. Advancements and Innovations in Automotive Wiring Harness Terminals
A. Introduction to Advanced Terminal Designs
As automotive technology continues to evolve, so do the designs of terminals used in automotive wiring harnesses. Manufacturers are constantly developing advanced terminal designs to meet the evolving needs of the industry. These advanced terminals incorporate innovative features and technologies to enhance performance, reliability, and ease of installation.
New terminal designs often focus on improving factors such as conductivity, durability, vibration resistance, and environmental protection. They may include features like enhanced contact surfaces, specialized coatings, or unique shapes that optimize electrical performance and ensure secure connections.
B. Miniaturization of Terminals for Space-Saving Applications
With the increasing complexity of automotive systems and the growing demand for compact designs, miniaturization of terminals has become a significant trend. Miniature terminals allow for more efficient use of space within the wiring harness, enabling engineers to accommodate additional components and functions in the vehicle without compromising on wiring integrity.
These smaller terminals are designed to maintain high conductivity while occupying minimal space. They often incorporate advanced crimping techniques and materials to ensure reliable connections despite their reduced size. The miniaturization of terminals enables greater flexibility in vehicle design and supports the integration of advanced electronic systems.
C. Waterproof and Weather-Resistant Terminal Solutions
Automotive wiring harnesses are subjected to various environmental conditions, including moisture, humidity, and exposure to water. To address these challenges, manufacturers have developed waterproof and weather-resistant terminal solutions.
Waterproof terminals feature specialized seals and gaskets that provide a tight seal against water intrusion. These terminals are designed to prevent corrosion and maintain reliable electrical connections even in wet or humid environments. They are often used in areas such as exterior lighting, engine compartments, and underbody wiring.
Weather-resistant terminals go a step further by offering protection against a wider range of environmental factors, including dust, dirt, and temperature variations. They may incorporate additional coatings or materials that enhance their resistance to the elements, ensuring long-term durability and performance.
D. High-Temperature Terminals for Engine Compartments
Automotive engine compartments are exposed to high temperatures generated by the engine and other components. Standard terminals may not be able to withstand these extreme heat conditions, leading to degraded performance or even failure. To address this, high-temperature terminals have been developed specifically for engine compartments.
These terminals boast a construction that incorporates materials capable of withstanding elevated temperatures without compromising their electrical prowess. They are skillfully designed to exhibit resistance to the perils of heat, vibration, and the chemical exposures commonly encountered within engine compartments. By doing so, high-temperature terminals ensure that vital electrical connections remain steadfast and reliable in the context of critical engine-related applications, such as sensors, ignition systems, and fuel injection systems.
The realm of terminal design has undergone remarkable advancements, encompassing groundbreaking features such as miniaturization, waterproofing, and the capacity to withstand high temperatures. These innovations have brought about a substantial enhancement in the performance and dependability of automotive wiring harnesses. Not only do these cutting-edge improvements grant greater design flexibility, but they also fortify protection against environmental factors and bolster durability, specifically tailored to meet the rigorous demands of automotive applications. In light of the ever-evolving landscape of automotive technology, we can anticipate further strides in terminal design that will rise to the challenge of supporting the escalating demands imposed by modern vehicles.
VI. Future Trends and Challenges in Terminal Applications
A. Increasing Electrification in Vehicles and Its Impact on Terminals
The automotive industry presently finds itself amidst a significant upheaval as it gravitates towards vehicle electrification, exemplified by the mounting prevalence of electric and hybrid vehicles. Such a profound shift inevitably engenders both novel challenges and unprecedented opportunities within the realm of terminal applications.
Electric vehicles (EVs), in particular, necessitate terminals of robust constitution capable of adeptly managing high-voltage electrical systems, including battery packs, electric motors, and power electronics. The design of these terminals must be tailored to withstand intensified currents and voltages, thereby ensuring the indispensable virtues of safety and reliability inherent to EV applications.
Hybrid vehicles, which combine internal combustion engines with electric propulsion systems, also require terminals that can accommodate the integration of both conventional and high-voltage electrical systems. This integration introduces the need for terminals capable of handling different voltage levels and electrical architectures within the same vehicle.
B. Integration of Terminals with Advanced Vehicle Systems
The future of automotive technology will witness the integration of terminals with advanced vehicle systems, including autonomous driving, connectivity, and advanced driver-assistance systems (ADAS). These complex systems crucially hinge upon the flawless conveyance of electrical signals and data, rendering terminals an indispensable component of their functional apparatus.
Terminal applications will need to support the increased data communication requirements of connected vehicles. This entails the seamless fusion of terminals with advanced communication protocols such as Ethernet or CAN (Controller Area Network), thereby guaranteeing the reliable and expeditious transmission of data.
Furthermore, terminals will play a crucial role in ADAS, where sensors, cameras, and other components rely on precise and accurate electrical connections for real-time data processing and decision-making. Advanced terminal designs will need to support the demands of these systems, including high-speed data transfer, signal integrity, and resistance to electromagnetic interference (EMI).
C. Challenges in Terminal Design and Manufacturing
As terminal applications march inexorably towards further evolution, a slew of challenges materialize in the sphere of terminal design and manufacturing processes:
1. Size and Space Constraints: With the miniaturization of automotive components, terminals need to be compact yet maintain optimal electrical performance. Designing and manufacturing small terminals that meet stringent electrical requirements while ensuring durability and ease of installation pose challenges for engineers and manufacturers.
2. Material Selection: Terminal materials must exhibit high conductivity, durability, and resistance to environmental factors. Identifying and utilizing materials that meet these requirements, especially for specialized applications such as high-temperature or high-voltage terminals, can be a challenge.
3. Manufacturing Consistency: Achieving consistent quality in terminal manufacturing is crucial for ensuring reliable electrical connections. Maintaining tight tolerances, proper crimping techniques, and uniform coating applications require advanced manufacturing processes and quality control measures.
4. Compatibility with Existing Infrastructure: As automotive manufacturers transition to advanced terminal designs, compatibility with existing infrastructure, including connector housings and wire harnesses, becomes essential. Ensuring seamless integration between new terminals and existing systems is a challenge that requires careful design and engineering considerations.
5. Testing and Validation: Thorough testing and validation of terminal performance and reliability are necessary to meet industry standards and ensure long-term functionality. Developing efficient testing methods for various terminal types, including high-voltage terminals, can present challenges due to the specialized equipment and expertise required.
Meeting these challenges will require collaboration among automakers, terminal manufacturers, and industry stakeholders. By investing in research and development, leveraging advanced manufacturing techniques, and addressing the unique requirements of future automotive systems, terminal applications can continue to evolve and adapt to the changing landscape of the automotive industry.
In conclusion, terminals play a crucial role in automotive wiring harnesses. Their importance cannot be overstated, as they ensure secure and reliable electrical connections in vehicles. As we have explored the application of terminals in the automotive industry, it is evident that their proper use is essential for efficient and safe vehicle operation. By understanding and implementing the right terminals, we can enhance the performance and longevity of automotive electrical systems.